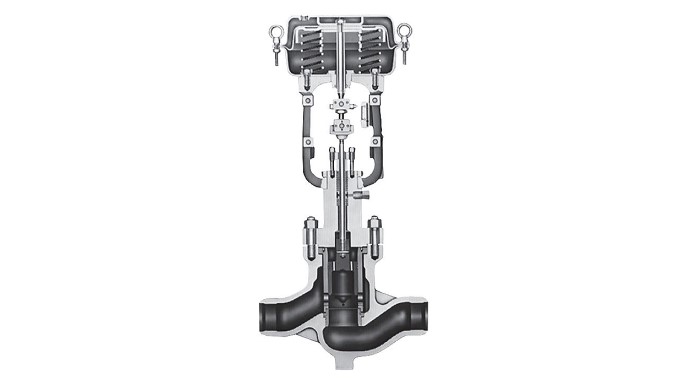
Cage-guided double-seated control valve that can be used in a wide range of applications up to a design temperature of 566 °C.
- Control valve for high temperature and high pressure service
- Main body structure with stabilizer for regulating fluid turbulence around the cage
- Compact overall due to the use of a small, high-output diaphragm motor even for high pressure differences
- Certified as SIL3-capable by exida Corporation
Structural drawing | Image
![]() |
---|---|
Valve type | Pressure balanced high-pressure cage type control valves |
Model No. | HPC_ _ _ |
Size | 1-1/2" to 8" |
Pressure rating | ANSI/JPI 900 to 2500 JIS63K |
End connection | Flanged : RF, RJ Welded : SW, BW |
Body material | Carbon steel |
Trim material | SCS24 304SS with Atomloy treatment 304SS with CoCr-A and Atomloy treatment |
Temperature range | -5 to 566°C |
Leakage performance | Class III |
Cv range | Class 1500 or less : 12 to 700 Class 2500 : 12 to 520 |
Range ability | 50:1 (option 75:1) |
Application | High temperature and high pressure steam of boiler and turbine unit for power plant and private power generation |
Option | - |
A wide range of material specifications
Products can be provided by using different materials for valve stems - e.g., carbon steel is generally used with water, steam, and fuel oil; and high corrosion resistant stainless steel that is essential for controlling corrosive fluids.
Corresponding to service
The excellent anti-cavitation performance of these cage valves plays an essential role in controlling fluids at high temperatures and under high differential pressures. Optional specifications can be applied to reduce aerodynamic noise produced by steam and gas.
Excellent seat leakage performance
Metal sheet tight shut (class III) are available.
Excellent external leakage prevention performance
A bellows seal can be added to valve stems. Increasingly sought-after specifications for gland packings can be applied to comply with fugitive emission regulations of volatile organic compounds.
High control performance
High control performance is achieved by a combination of wide rangeability and a smart valve positioner.
The original internal valve structure adopted by azbil essentially eliminated the shortcomings of conventional double-seated control valves that suffered from reversal of fluid reaction force, thereby achieving stable control.