
Reduced valve maintenance costs by combining TBM and CBM based on diagnostic data
Company in this case study
Industry | Petrochemicals Manufacturing, Company P |
Department | Equipment Maintenance Department |
Keywords
#Manufacturing DX #TBM #CBM #Equipment Maintenance #Maintenance Costs
Background
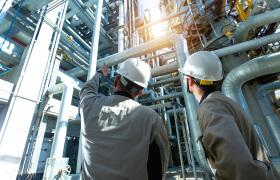
Company P, a long-established petrochemical manufacturer, was identifying current issues that needed to be resolved in order to promote DX at its manufacturing sites.
When a member of the Facilities Maintenance Department, who was in charge of the project, probed into a suggestion from upper management that there might be waste in valve maintenance operations, he found a problem.
Issues
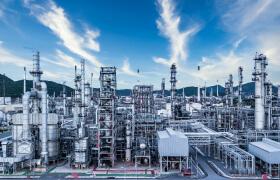
The rationale for valve maintenance operation rules is unclear. The field is reluctant to change due to concerns about increased labor.
Company P had divided a vast number of valves into three groups according to their importance in the manufacturing process, and was operating them under TBM (time-based maintenance) with open inspections at regular maintenance intervals of one, two, and four years, respectively.
Mr. E, DX Promotion Team Leader of the Facilities Maintenance Department, describes the reality of this situation.
"Even after spending man-hours to open and inspect valves during routine maintenance, many valves were normal, resulting in unnecessary maintenance costs. The valve maintenance operation flow has been inherited from what was decided decades ago. The rationale for grouping and TBM cycles, etc., is now unclear as to whether it matches the actual situation."
On the other hand, one of the problems was that when abnormalities were found in valves during open inspection, replacement parts could not be arranged in time for the scheduled maintenance period. In such cases, the facility would have to be shut down again for maintenance when the parts were available, or wait until the next scheduled maintenance.
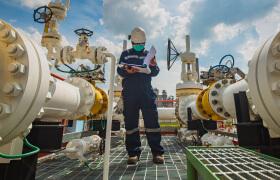
The team decided to review the TBM cycle as an improvement plan and to consider DXing to reduce maintenance costs by optimizing maintenance targets, including a partial shift to CBM (Condition Based Maintenance). However, there was no objective data on which to base the review. In addition, there were negative opinions in the field, such as whether DXing would increase unnecessary work, and we were unable to take concrete steps to implement improvement measures.
Mr. E and his team members began to grow impatient as they could not find a solution to the difficult problem of DXing in order to reduce maintenance costs.
Key Points of Issue
- Image
Valve maintenance operations were operated according to rules set decades ago.
- Open inspection by TBM had issues such as waste and lost maintenance opportunities due to delays in parts delivery
- There was resistance in the field due to concerns about the increased effort required by DXing.
Key Points of Solution
- Image
Ongoing data collection, analysis, and diagnosis of valves allowed us to establish a well-founded maintenance cycle.
- Knowing the signs of abnormality in advance, and being able to plan for scheduled repairs by combining TBM with CBM
- Generous support has eliminated on-site resistance to DXing.
Solution
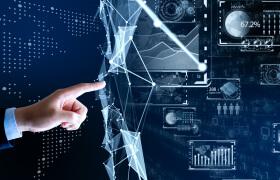
Reviewed all maintenance operation rules based on valve diagnostic data and reduced maintenance costs by approximately 20 million yen per year.
While gathering information, Mr. E attended a study group of his peers and heard about Azbil's valve analysis and diagnosis service (Dx Valve Cloud Service) and became interested in it. He immediately contacted Azbil to discuss his company's issues.
The Dx Valve Cloud Service was a DX service for the manufacturing industry that allows users to check and manage valve health in the cloud. It continuously collects operational data for each valve and automatically analyzes and diagnoses. The results can be checked on the web, and maintenance operations can be performed by CBM based on the diagnosis results.
The ability to monitor signs of valve abnormalities in advance and to optimize the valves that need maintenance by combining the CBM with the scheduled maintenance planned by the TBM has been well received by our peers. Also, by monitoring the signs of abnormality, it would be possible to perform maintenance as planned for the scheduled maintenance if the necessary parts for countermeasures are prepared in advance.

We expected that Azbil would not only provide diagnostic tools, but also support us in planning maintenance plans based on the automatically provided diagnostic results, thereby eliminating the resistance of manufacturing sites to DX, which we felt would increase the time and effort required for maintenance.
Mr. E and his team submitted a proposal to upper management to optimize valve maintenance operations and promote DX at the manufacturing site by introducing the Dx Valve Cloud Service, and received approval. With Azbil's cooperation, they immediately implemented the service, collected valve operation data, and began reviewing valve maintenance operation rules based on the diagnostic results.
For valves with a short maintenance cycle and a tendency to have abnormalities, the maintenance cycle was optimized by comparing diagnostic data with the results of actual open valve inspections and reviewing the diagnostic thresholds that form the basis for determining whether or not maintenance is necessary. For valves with a long maintenance cycle and no tendency for abnormalities to occur, the maintenance cycle was further lengthened based on the fact that "no signs of abnormality were observed," and some valves were shifted to CBM where temporary maintenance is performed only when signs of abnormality are detected.
By implementing these measures for all valves, we succeeded in revising the valve maintenance operation flow that had been used for several decades. Based on this, valve maintenance operations were optimized, and it was expected that maintenance costs could be reduced by approximately 20 million yen per year.
Since DX at the manufacturing site will also stabilize production facilities and strengthen security, it has been decided to expand the system to other plants, and Mr. E and his team are busy making preparations.
Services that solved this issue
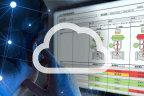
Cloud-based valve analysis and diagnostic service
Dx Valve Cloud Service
x Valve Cloud Service automatically transmits and analyzes valve operating data collected by the control valve maintenance support system PLUG-IN Valstaff (hereinafter referred to as "Valstaff") on the cloud, and provides valve analysis and diagnosis results via web content on the cloud. This is a service that provides valve analysis and diagnosis results via web content on the cloud.
Other case studies
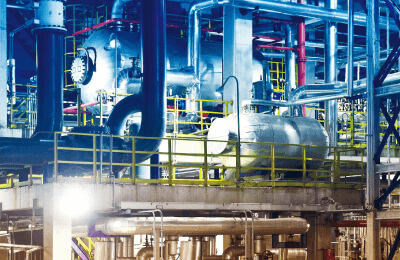
Company F, a petrochemical materials manufacturer, is facing the challenge of passing on maintenance skills to younger engineers as skilled engineers are retiring from active service. We will introduce how DX has been utilized in the manufacturing industry to enable data-backed valve maintenance operations.
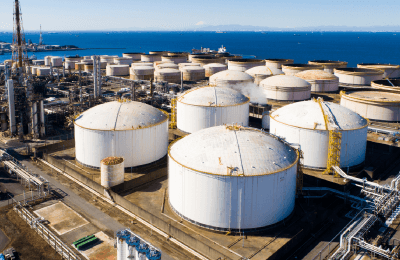
Want to avoid sudden valve failures that lead to plant shutdowns and reduced product quality...
After hearing about an emergency shutdown of equipment at a neighboring plant caused by a valve malfunction that resulted in major damage, U, a petrochemical materials manufacturer, decided to review its own maintenance operations. See how the introduction of a DX service for the manufacturing industry that can monitor signs of abnormalities in the valve that caused the problem led to stable plant operations.
Inquiries