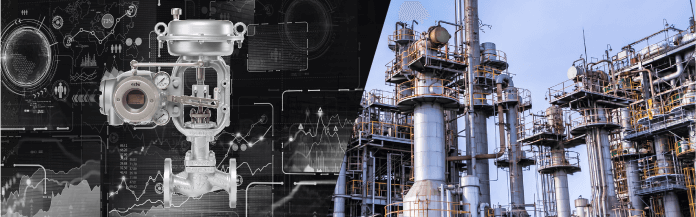
Use cases Customers and results Results
We are making an increasing number of diagnoses on a diverse array of valves at a wide range of plants.
Use cases
Industry | Equipment |
---|---|
Petroleum, gas | Hydrodesulfurization equipment |
Heavy fraction cracking equipment | |
Off-site facility equipment | |
LNG equipment | |
Petrochemicals, chemicals | Ethylene equipment |
Ethylene oxide equipment | |
Phenol equipment | |
Bisphenol equipment | |
Styrene monomer equipment | |
High-pressure polyethylene equipment | |
Low-pressure polyethylene equipment | |
Polypropylene equipment | |
Methyl methacrylate equipment | |
Cyclohexane equipment | |
Aromatic hydrocarbon equipment | |
Vinyl chloride monomer/resin equipment | |
Rubber equipment | |
Fluorine equipment | |
Electrolytic/caustic soda equipment | |
Film-related equipment | |
Various functional product manufacturing equipment | |
Iron and steel | Cold rolling equipment |
Ceramic engineering | Glass and cement equipment |
Food | Mixing vessels |
Boilers | |
Semiconductors | Air-conditioning units |
Social infrastructure | Garbage disposal facilities |
Utilities | Power plants (steam etc.) |
Sewage facilities | |
Water supply facilities |
A must-see for those tasked with site improvement
- Utilization of a Valve Diagnosis Service to Enhance Safe Operation of Power Generation Facilities (case study)
- Dramatic Efficiency Improvement in Valve Loop Checks During Regular Maintenance (case study)
- Optimize Maintenance Timing by Understanding the Tendency of Valves to Stick in the Acrylate Monomer Polymerization Process (case study)
Give some examples of how valve analysis and diagnosis prevented negative impact on plant operation.
How has valve diagnosis helped to promote DX at manufacturing sites?
Give an example of problem detection in a key valve of a boiler facility.
For a limited time, we disclose the latest trends and examples of valve analysis and diagnosis, which have undergone innovation through the use of information technology.
Customers and results
Daikin Industries, Ltd., Kashima Plant
The Daikin Industries Kashima Plant, which produces fluorochemical products for a industry, has recently focused on effective maintenance of control valves. The failure of a control valve has a greater impact on production than the failure of other instrumentation equipment used in plant operations, and control valves require large repair costs even in the course of regular maintenance. By switching from periodic maintenance to condition-based maintenance of these valves, the Kashima plant has significantly reduced maintenance costs and has established a system for quick handling of minor malfunctions and warning signs of future problems.
Ibaraki Plant, Mitsubishi Chemical Corporation
Monitoring of valve conditions using cloud services supports the safe operation of large-scale petrochemical plants.
NS Styrene Monomer Co Ltd Oita Works
With styrene monomer as its main product, NS Styrene Monomer Co., Ltd. (NSSM) meets a wide range of industrial needs. After repeated valve failures, the company’s Oita Works plant is now introducing smart valve positioners. The plant is also using a system to improve the monitoring of valve status. In this way, by providing a mechanism to track valve failure trends, a high level of plant operation stability is being achieved.
Showa Denko K.K., Kawasaki Plant
Showa Denko’s Kawasaki Plant in Ogimachi boasts a long history of development and manufacture of organic and inorganic chemical products. In order to promote smart industrial safety using technology such as the Internet of Things (IoT), the company pays special attention to valves, which are indispensable for production. To optimize maintenance work and reduce costs, Showa Denko utilizes Azbil’s smart valve positioners, valve diagnostic systems, and valve analysis and diagnosis services provided by specialist engineers.
Results
Value

Value1
Preventing sudden equipment shutdown
Collecting diagnostic data and monitoring trends during plant operation helps to prevent the deterioration of control valves, which was previously difficult to detect, and their sudden failure, which can cause unplanned shutdowns.

Value2
Optimizing maintenance plans (to TBM + CBM)*
With proper diagnosis of valve operating condition, the selection of valves to overhaul can be optimized.
* Time-based maintenance + condition-based maintenance

Value3
Faster equipment startup after periodic maintenance
Labor-intensive testing after periodic maintenance can be streamlined to accelerate equipment startup.
And more…

Diagnostic possibilities with the Smart Valve Positioners 700 Series
Adding to the functionality of the previous valve positioners (the 300 Series), Smart Valve Positioners 700 Series can also measure the motion of the control valve from different angles using built-in air pressure sensors. That allows diagnosis of underperformance and establishment of operational benchmarks before valves start working abnormally.
Inquiries