Diagnose underperformance and establish operational benchmarks before valves start operating abnormally
Despite no clear signs of abnormality, are valves working correctly and delivering proper performance?
On top of the same functions offered by the previous generation of valve positioners (the 300 Series), the Smart Valve Positioners 700 Series also enables you to measure the motions of control valves from different angles using built-in air pressure sensors. More advanced evaluation, such as diagnosis of underperformance and establishment of operational benchmarks, can be made before valves start working abnormally.
Checking the condition of underperforming valves
A maximum friction diagnosis parameter enables you to check valves for underperformance while their operation is still in the normal range. Abnormalities that cannot be detected using information from angle sensors can also be checked.
Diagnostic range of the 700 Series*
Valves are checked for underperformance using the maximum friction diagnosis parameter when they are not yet operating abnormally
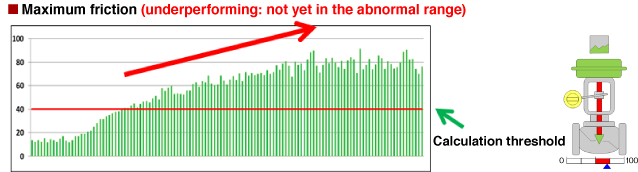
Diagnostic range of the 200/300 Series*
No abnormality, according to information from angle sensors
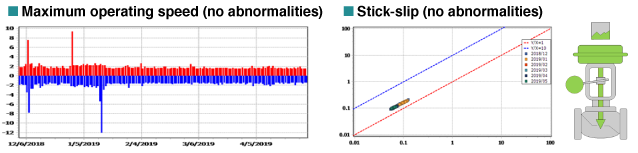
Checking valve operational performance
Valve performance is assessed during operation by monitoring output air pressure and degree of opening.
In the current operating condition, the valve cannot be fully closed in an emergency
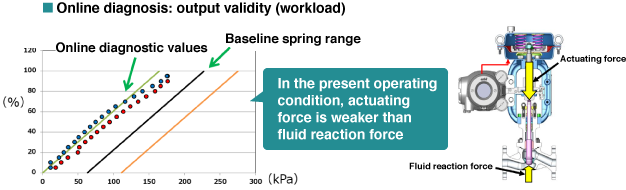
Related Products
A must-see for those tasked with site improvement
- Utilization of a Valve Diagnosis Service to Enhance Safe Operation of Power Generation Facilities (case study)
- Dramatic Efficiency Improvement in Valve Loop Checks During Regular Maintenance (case study)
- Optimize Maintenance Timing by Understanding the Tendency of Valves to Stick in the Acrylate Monomer Polymerization Process (case study)
Give some examples of how valve analysis and diagnosis prevented negative impact on plant operation.
How has valve diagnosis helped to promote DX at manufacturing sites?
Give an example of problem detection in a key valve of a boiler facility.
For a limited time, we disclose the latest trends and examples of valve analysis and diagnosis, which have undergone innovation through the use of information technology.
Inquiries