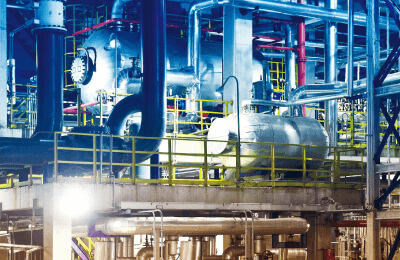
Experience and know-how can be corroborated by diagnostic data
What is the optimization of valve maintenance operations using DX (Digital Transformation) in the manufacturing industry?
The company in this case study
Industry | Petrochemical Manufacturer, Company F |
Department | Maintenance Department |
Keywords
#ManufacturingDX #MaintenanceOperations #AnomalyPrediction #StableOperations
Background
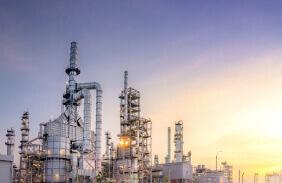
Company F boasts a high market share in the field of chemical-based materials.
Company F has responded to the demands of orders coming in from all over the world while revising its production plan several times.
However, as skilled engineers increasingly retire from active service, certain concerns have come to light regarding the transfer of maintenance skills to younger engineers.
Issues
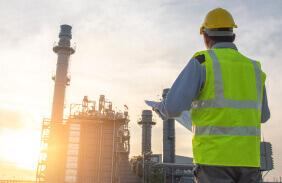
Experience is difficult to quantify and verbalize, and it belongs to the individual. Passing on skills to younger workers is a major challenge.
The maintenance department was concerned about the excessive reliance on the experience of skilled engineers for valve maintenance tasks and abnormality assessments. Although we still conduct valve inspections based on a maintenance cycle set a few years ago, this cycle was determined long ago based on the engineers' experience. Currently, the rationale for this cycle is unclear.
Mr. H from the maintenance department looked back on that time and said the following.
"During valve inspections, we visually checked and assessed the condition inside the valves, and took photos to accumulate information on wear and damage trends. However, with photo-based information, which is just a 'snapshot,' the criteria for assessment can vary from person to person. Additionally, with such information alone, it was challenging for younger staff to make maintenance decisions, such as changing the maintenance cycle."
If an abnormality occurs in a valve while the equipment is in operation, the issue only becomes apparent when it affects the process. At that point, we start investigating the cause and often determine that the valve is the culprit. While numerous troubleshooting experiences help accumulate knowledge and expertise, such opportunities are very rare.
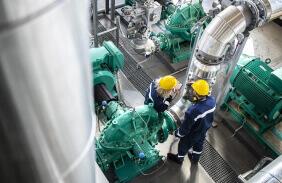
"Quantifying and verbalizing experience and know-how is difficult, making it highly personalized. While passing on skills to younger staff is a major challenge, in recent years, digital transformation (DX) has become an unavoidable issue in the manufacturing industries, including the oil and chemical sectors," said Mr. H.
"Within Company F, there has been a strong call to promote digital transformation (DX), and the maintenance department also wanted to leverage DX to optimize valve maintenance operations and create new value."
However, specific, easy-to-understand, easy-to-use DX tools for manufacturing and suggestions for them were hard to find. The day of retirement for these skilled engineers was rapidly approaching, as they searched and searched but could not find anything suitable.
Key Points of the Issue
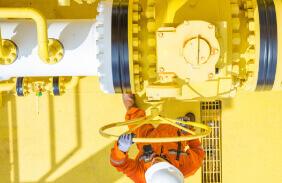
- Too much reliance on the experience of skilled engineers for valve maintenance work and abnormal judgment
- When inspecting openings, the criteria for judgment may differ from person to person based on only "point" information in the form of a photograph.
- In the manufacturing industry, such as the petroleum and chemical industries, passing on skills to younger workers and DXing were major issues.
Key Points of Solution
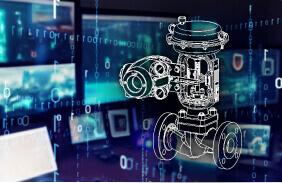
- Everyone can now use a common criterion, diagnostic data, to determine how to maintain valves.
- Experience + data now allows important skills to be passed on to future generations.
- Azbil's generous support made it possible to expand to other plants and promote DX.
Solution
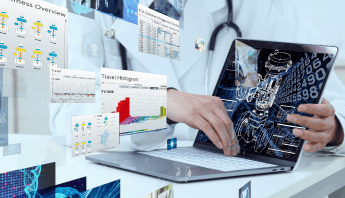
Linear" information is added to "point" information! Experience + data to pass on important skills to future generations
While gathering information to solve the problem, Mr. H found information on Azbil's valve analysis and diagnosis service (Dx Valve Cloud Service) through a web search. Azbil's Dx Valve Cloud Service is a cloud-based valve analysis and diagnosis service, a tool to check and manage the health of valves through web content on the cloud. Mr. H remembered that a case study of this service had been circulated within the company as a reference material, so he immediately contacted the sales representative.
After confirming the details, we learned that Azbil's Dx Valve Cloud Service enables us to constantly check the diagnostic results of valves analyzed weekly on the cloud, and to develop maintenance plans based on the latest valve analysis diagnostic results. In addition to providing tools, they also provide support for the use of diagnostic data.
After much internal discussion and approval from upper management, Company F decided to implement Azbil's Dx Valve Cloud Service. We immediately asked Azbil for support, and the support system was very generous, and they were able to provide us with advice on countermeasures for valves that showed abnormalities based on the diagnostic data.
The "line" of continuous diagnostic data has been added to the "point" of information we had before. As a result, everyone can now judge valve maintenance methods based on a common standard, rather than relying solely on experience and know-how.
The accumulated experience and know-how can now be corroborated with diagnostic data, which is an effective service for passing on maintenance skills. I am relieved that we can now pass on important skills to future generations based on experience plus data.
Now that the company has achieved stable and reliable maintenance operations, it has asked Azbil to help it further expand its operations to other plants and further promote the use of DX./strong>
Services that solved this issue
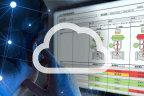
Cloud-based valve analysis and diagnostic service
Dx Valve Cloud Service
x Valve Cloud Service automatically transmits and analyzes valve operating data collected by the control valve maintenance support system PLUG-IN Valstaff (hereinafter referred to as "Valstaff") on the cloud, and provides valve analysis and diagnosis results via web content on the cloud. This is a service that provides valve analysis and diagnosis results via web content on the cloud.
Other case studies
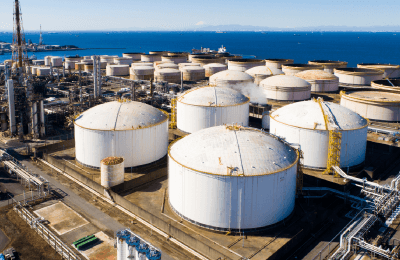
Want to avoid sudden valve failures that lead to plant shutdowns and reduced product quality...
After hearing about an emergency shutdown of equipment at a neighboring plant caused by a valve malfunction that resulted in major damage, U, a petrochemical materials manufacturer, decided to review its own maintenance operations. See how the introduction of a DX service for the manufacturing industry that can monitor signs of abnormalities in the valve that caused the problem led to stable plant operations.

We tried to take a scalpel to the TBM operating rules that had been untouched for decades...
Company P, a petrochemical manufacturer, decided to review its valve maintenance operations, which had been inherited for several decades. We will introduce the process of shifting from the old customary operation to the optimal valve maintenance operation based on data.
Inquiries