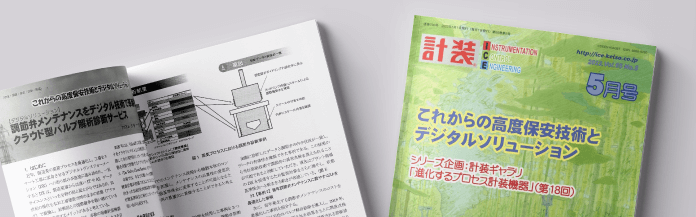
『調節弁メンテナンスをデジタル技術で革新するクラウド型バルブ解析診断サービス』に関しての記事が月刊「計装」に掲載されました。
報道記事:月刊誌「計装」 2022年5月号
調節弁メンテナンスをデジタル技術で革新するクラウド型バルブ解析診断サービス
1.はじめに
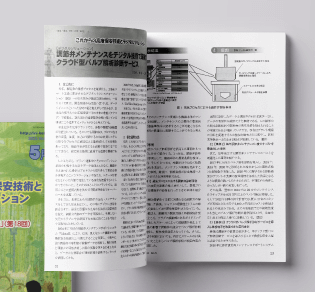
近年、製造業の業務プロセスを最適化し工場をスマート工場に変身させるデジタルトランスフォーメーション(DX)への取り組みが急速に進み始めた。一見するとDXは、製造現場からは遠いITやAI、データサイエンスといった分野の話と捉えがちではあるが、21世紀の現代もなお工場建設当時のままの状態(アナログ)で稼働し、新興国との国際競争を戦い続けている現場にこそ適用するメリットがあると考えている。
石油化学や化学プラントでは、多数の現場計装機器が設置されている。その中でも調節弁は、プロセスを目標の流量、温度、圧力に制御するために制御システムの指令をプロセスに直接伝える最終端としての役割を担っており、機能不全が生じると品質や効率の低下だけではなく、安定安全操業に直結する重要な機器である。しかしながらプラント運転中にそのコンディション状況を把握する方法やデータはほとんど無く、機能不全と疑われた場合はプロセスから取り外して開放点検を実施することでエロージョンや詰まり、スケール付着などといった内部で発生している症状を把握することしかできなかった。そのためほとんどのプラントでは、調節弁ごとに整備周期を決めて時間基準保全でオーバーホールを実施している。
当社では、長期にわたり調節弁の販売・メンテナンスをしてきた知見を活かし、その中にデジタル技術を融合させた。操業に影響を与え始める以前に異常兆候を捉え、調節弁内部のデータを可視化し、予期しない突発のトラブルや効率低下を未然に防ぐことを可能とする取組みをしている。2004年に初代の調節弁メンテナンスサポートシステムValstaffにより、従来、見えなかった調節弁の稼働状況を数値化し可視化することを実現し、十数年に渡り調節弁の専門家が稼働データを解析し、解析結果と調節弁の開放点検した際の実態を突き合わせしながら、データから調節弁の健康状態を診断するノウハウを蓄積してきた。2020年には、Valstaffに収集した調節弁の稼働データをクラウドシステム上に自動送信し、十数年かけて蓄積してきた専門家のノウハウを使って調節弁の健康状態を自動で診断するクラウド型バルブ解析診断サービスDx Valve Cloud Serviceをスタートさせた。
本稿では、今までは難しかった調節弁の稼働状況や健康状態が把握できるようになることで、整備周期の決まった伝統的な時間基準での調節弁メンテナンスを、状態基準保全に移行していくフェーズについて事例を用いながら紹介する。
2.保全運用の変革
現在、日本の多くのプラントはイベントドリブン型といわれ、あらかじめ作成したプログラムのもと、人が属人化することで成り立つシステムが散見される。しかし、このシステムは時代の変化にともない、システムが複雑化した場合など「デジタル化の足かせ」の要因となりアジリティの高い働きをすることは難しい。また少子高齢化が急速に進む日本において、技術や知見を継承する必要がある人材育成面でも課題となっている。
当社では時代の変化に追従するため、プラントに点在している既存のデータが「必要とされるIT環境」となるよう、連続的にITを進化させていくDXを目指している。このレガシーシステムから脱却する活動は、データドリブン型プラント運転として様々な種類のデータや情報をビックデータにかけデータの蓄積と分析を行い、プラント状況や経営指標などを可視化し、意思決定に繋げられるようなソリューションとして提供している。調節弁においてはValstaffを活用し、リアルタイムで運転状況と機器本体のコンディション状況を監視している。また診断している調節弁はレーダーチャートのように可視化され、様々な角度から分析された結果をレポートとして出力することもできるため、プラントの運転状況と機器本体の負荷状況などを比較した検討などを実施することも可能である。そのため、これまでの先人の方々の知見や経験のもとで確立してきた伝統的な時間基準でのメンテナンス周期から機器本体のコンディションを把握し、メンテナンスの必要性の意思決定をする状態基準保全に変革することが可能となるため、保全費用の最適化に貢献することができると考えている。
3.診断事例
今回、当社のバルブ解析診断を活用した事例を三つのフェーズに分けて紹介する。一つ目は、調節弁診断評価・実行事例として、機器単体の異常兆候を検知した導入事例。そして二つ目は機器だけではなく装置全体に有効性を見出し、メンテナンス周期を見直すことに成功した事例。最後に、診断業務が保全業務へと適用することができた運用事例である。
3.1【事例1】蒸気プロセスにおける調節弁診断事例
まず始めに調節弁診断の導入事例として、蒸気プロセスにおける調節弁の診断を行ったときの事例を紹介する。調節弁の解放整備をする前に対象となる調節弁の解析診断を実施した結果、シャフトの摺動性とトリムの詰まりに異常が発生しており開放推奨判定となっていた。その結果を踏まえ、調節弁の開放点検と比較検証作業を実施したところ、プラグの摺動部にあるガイドリングの内壁に付着したスケールによって摺動傷が発生しており、この傷の影響で摺動性の部分でバルブ解析診断が異常と判断し、解放推奨判定となっていた。更にトリムの詰まり判定においても、内弁にスケールの付着が発生していたことからバルブ解析診断の判定内容の整合性を確認した。実際に診断したデータと調節弁の内弁状況が一致しデータの有効性を確認できた事例である。この結果から当社診断技術で調節弁の異常兆候を捉えられることが可能であると判断していただき、現在はプラント現場のDXを促進するため監視対象をさらに増やし状態基準保全へと舵をきる動きが加速している。(図1)
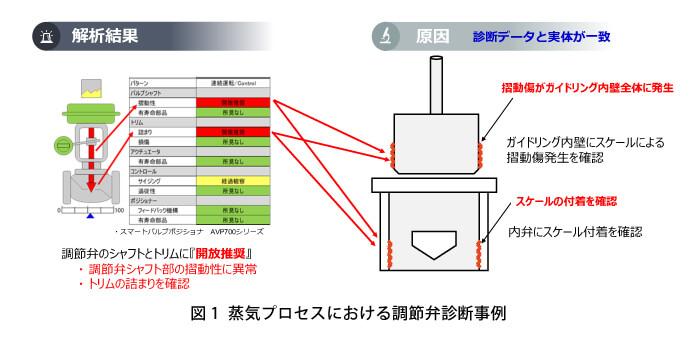
3.2【事例2】毎年調節弁メンテナンスに費やすコストを最適化した事例
次に毎年発生する調節弁メンテナンスのコストを最適化した事例を紹介する。2017年に当社のバルブ解析診断を導入し、2018年、2019年、2020年と診断された結果をもとに開放点検と比較検証を実施した。2020年には解析される診断結果がプラントや装置の設置環境を加味した結果となるような精度の高いものとするために、各調節弁の条件に合ったしきい値の見直しを行った。その結果、翌年の2021年に25台のメンテナンスをスキップさせ970万円以上のコスト削減を実現した。そして2022年以降の保全計画では、既に43台のスキップが可能となる予定で2,400万円程度のコストが削減されるとの見込みである。また今後建設予定の新規装置にも当社のバルブ解析診断が標準採用となり、生産性向上及び保安力強化に貢献している。(図2)
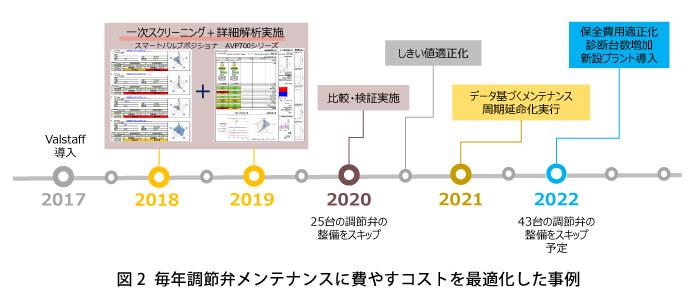
3.3【事例3】クラウド型バルブ解析診断サービスを導入し業務効率を改善できた運用事例
最後は調節弁の設置台数が多く、本クラウド型バルブ解析診断サービスを導入することで業務効率を大幅に改善できた事例である。2016年に弊社調節弁メンテナンスサポートシステムValstaffの導入は完了していたが上手く活用されておらず、保全業務は先人の方々の知見や経験により作り上げられた時間基準でのメンテナンス周期となっていた。しかし開放点検を実施するも、その中の6割程度が「問題なし」という結果となるため、過剰整備の懸念があった。しかし、これまで確立してきた時間基準でのメンテナンス周期(2年に1回)を覆すような状態基準保全への切り替えは、前例がないことから変革を行うことに難色を示していた。そして2020年頃、お客様社内で大幅な保全費用見直しの議論があり、当社の診断サービスは状態基準保全への変革の足掛かりになるのかということで、開放点検結果の比較検証を実施させて頂いた。その結果、診断で「良好」と判断された調節弁は不具合箇所もなく診断データと実体が一致していたため、メンテナンス周期をスキップすることに成功した。その後、当社から自動で診断するクラウド型バルブ解析診断サービスDx Valve Cloud Serviceがリリースされ、接続台数が多く、監視や診断される結果を見て判断する負荷を軽減するために導入を決定し、日常業務やコロナ禍においての在宅勤務時にもWeb上で確認できるようになったことから業務の効率化を実現することがでた事例である。(図3)
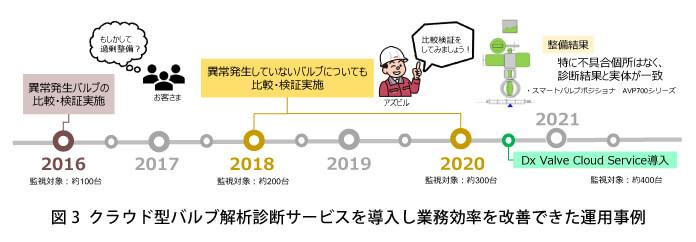
4.おわりに
本稿では、現在、当社でサービスを開始して1年を経過したクラウド型バルブ解析診断サービスDx Valve Cloud Serviceの事例を交えて、調節弁メンテナンスの時間基準保全から状態基準保全へ移行していくフェーズについて紹介した。
今、現在もDx Valve Cloud Serviceには、プラント運転中の調節弁に係わるデータが24時間365日収集されており、これらはビッグデータとなりつつある。今後は、この調節弁の健康状態に係わるビッグデータを、80年蓄積してきた調節弁メーカとしての技術と、長年に渡り調節弁メンテナンスサービスを提供させていただいてきた現場のノウハウ、そしてデータサイエンス技術を組み合わせることによって、より価値のあるサービスへと発展させていきたい。また、このクラウド環境を調節弁の健康状態の診断に留まることなく、診断結果に基づく推奨部品のリストアップから手配オーダーの自動化や、調節弁のライフサイクル(新品納入~廃棄までの一生)に渡る保全来歴管理など調節弁メンテナンス業務をデジタル技術で革新するプラットフォームに発展させたいと考えている。
そしてその先には、クラウド上でIBM MaximoやSAP PM、富士通PLANTIAなど CMMS やEnterprise Asset Managementとつながることによって、今までであれば時間基準の長期レンジで作られている保全計画が、状態基準でダイナミックに計画されるようになることが考えられ、製造業オーメーションピラミッドのセンサー/アクチュエーターのレベル1~Enterpriseのレベル4までをダイナミックに連動したDX時代の設備管理オペレーションの姿が創造される可能性があると考えている。
注)
- 「Valstaff」は、アズビル株式会社の商標です。
- Maximoは、世界の多くの国で登録されたInternational Business Machines Corp.の商標です。
- SAPはドイツにあるSAP SEやその他世界各国における商標または登録商標です。
- 掲載中の会社名、団体名、技術名、および製品名は、各社または各団体の商標または登録商標です。
〈参考文献〉
1)曽禰寛純:IoT技術活用によるスマート保安《 熟練運転員の叡智を継承・超越 》、平成29年1月27日 未来投資会議説明資料 資料2(PDF)
2)経済産業省 保安課:スマート保安先行事例集~安全性と収益性の両立に向けて~、平成29年4月(PDF)
3)亀井宏和:自主保安の高度化に貢献するスマートバルブ診断、計測技術2018年8月号
4)山﨑史明:生産設備の安定化・保安力強化に向けたクラウド型バルブ解析診断サービス、計装2021年3月号
5)朝日秀介:化学プラントにおけるバルブ/ポジショナーのリモート解析診断~その取り組みと評価、計装2021年8月号
引用元
- 計装 2022年5月号(有限会社 工業技術社)
システム・サービスに関するお問い合わせ